Unterm Hammer: der DATOGRAPH PERPETUAL im Prüflabor: Unterschied zwischen den Versionen
WWWIG (Diskussion | Beiträge) K (Vorlage andere Sprachen in Interwikis getauscht) |
|||
Zeile 1: | Zeile 1: | ||
'''Unterm Hammer: der DATOGRAPH PERPETUAL im Prüflabor''' | '''Unterm Hammer: der DATOGRAPH PERPETUAL im Prüflabor''' | ||
− | + | ||
[[Bild:Lange Datograph-Perpetual.jpg|thumb|Lange Datograph-Perpetual (Platin), Ref. 410.025]] | [[Bild:Lange Datograph-Perpetual.jpg|thumb|Lange Datograph-Perpetual (Platin), Ref. 410.025]] | ||
Zeile 26: | Zeile 26: | ||
[[Kategorie:Nachrichten 2008]] | [[Kategorie:Nachrichten 2008]] | ||
+ | [[en:Under the Hammer: The DATOGRAPH PERPETUAL in the Test Lab]] |
Version vom 17. August 2011, 07:04 Uhr
Unterm Hammer: der DATOGRAPH PERPETUAL im Prüflabor
Glashütte, Oktober 2008
Bei einer Uhr von A. Lange & Söhne darf man erwarten, dass sie länger lebt als ihr Besitzer. Deshalb durchlaufen alle neuen Modelle einen der härtesten Tests in der Uhrmacherei. Auch die kompliziertesten, wie der DATOGRAPH PERPETUAL.
Jeder Uhrenliebhaber würde dieses Modell am liebsten in einem Tresor verschließen und nur mit Handschuhen anfassen, wenn er es herausholt: einen DATOGRAPH PERPETUAL von A. Lange & Söhne. Mit der genialen Kombination aus Flyback-Chronograph und ewigem Kalendarium ist er eine Uhr für den Augenblick und für die Ewigkeit und eines der kompliziertesten Kaliber, die die traditionsreiche Manufaktur aus Sachsen seit der Neugründung vor 18 Jahren herausgebracht hat.
Christoph Schlencker dagegen nimmt die Uhr nicht einmal vom Handgelenk, wenn er seinen Garten umgräbt oder den Fußboden seines Wohnzimmers verlegt. Denn sein Beruf ist es zu sehen, wie viel diese Uhr aushalten kann und wie stabil ihre einzelnen Komponenten sind und wie präzise das Ganze noch arbeitet, wenn man damit etwas macht, was man in der Praxis besser vermeiden sollte. Zum Beispiel: den DATOGRAPH PERPETUAL aus einem Meter Höhe fallen zu lassen. Beim Schlagtest passiert genau das, die Uhr wird einem standardisierten Hammerschlag ausgesetzt, der exakt einem Fall aus einem Meter Höhe auf einen Hartholzboden entspricht. Dabei treten für die Teile kurzfristige Belastungen auf, die dem 5.000-fachen ihres eigenen Gewichts gleichkommen. Anders gesagt: Ein Werksteil, das normalerweise ein Gramm wiegt, ist in diesem Sekundenbruchteil fünf Kilogramm „schwer“ – und muss das aushalten.
Schlenckers Ziel ist es zu erreichen, dass der DATOGRAPH PERPETUAL nach solch einer „Misshandlung“ immer noch funktioniert. Denn in punkto Robustheit und Zuverlässigkeit muss jede A. Lange & Söhne die gleichen Anforderungen erfüllen. Er sucht nach Verbesserungsmöglichkeiten in der Konstruktion oder im Material und schaut, wo man in der Fertigung vielleicht noch etwas verändern kann. Er ist der Leiter des Prüflabors. Es ist eine der wichtigsten Positionen im Unternehmen. Man kann nicht sagen, dass es auch immer eine der beliebtesten ist. Denn ein Teil seiner Aufgaben besteht darin, den Kollegen das Leben so schwer wie irgend möglich zu machen. Alles, was sich die Konstrukteure ausdenken und der Musterbau zusammenschraubt, versucht er wieder zu zerstören. Er sucht die Schwachstellen in jedem Entwurf. An seinem kritischen Auge muss jede neue Idee vorbei. Es gibt keine Uhrenkonstruktion, die ohne seine Prüfung in die Fertigung geht.
Schlencker hat das Labor vor acht Jahren selbst aufgebaut. Als die Manufaktur damals jemanden für diese Aufgabe suchte, griff der gelernte Uhrmacher sofort zu. Es war der Job, auf den er sein ganzes Leben gewartet hatte. Denn bei Lange sollte es darum gehen, die schärfsten Qualitätskontrollen zu etablieren, die es in der gesamten Feinuhrmacherei gibt. Eine Art Crashtest-Labor sollte entstehen wie in der Automobilindustrie, ein Ort, an dem Hightechprodukte ihr letztes Feintuning bekommen. Im Grunde sollte das Prüflabor gar kein Ort der Zerstörung sein. Sondern einer der Forschung. Einige Geräte dafür gab es seinerzeit zu kaufen, andere Tests hat er selbst entwickelt. Zum Beispiel den Rütteltest. Er besteht im Wesentlichen aus einer einfachen Holzkiste, die in alle denkbaren Positionen rotiert, vor und zurück, schräg und mit Überschlag und das in einer unregelmäßigen Geschwindigkeit. Dabei rumpelt im Innern eine Uhr vier Mal pro Sekunde gegen die Wand, und nach 24 Stunden sieht das Exemplar aus, als hätte jemand damit den Nanga Parbat bestiegen. „Der Rütteltest simuliert fünf Jahre Nutzung durch einen sportlichen Träger“, sagt Schlencker dazu. Nach dieser Tortur müssen alle 556 Uhrwerksteile des DATOGRAPH PERPETUAL noch fest an ihrem Platz sitzen und alle Funktionen einwandfrei arbeiten.
Danach entwickelte er ein „Drückertestgerät“, das er soweit modifizierte, bis es die Langzeitbeständigkeit der Uhr in einer realitätsnahen Simulation untersuchen konnte. Von Weitem sieht es aus wie eine riesige Spinne.
Aus der Nähe besteht es aus kleinen Bolzen, die immer wieder die Drücker am DATOGRAPH PERPETUAL schalten, und diese müssen dann auch nach je 50.000 mal Start, Stopp, Nullstellung und Flyback genauso präzise und mit dem gleichen Widerstand arbeiten wie am ersten Tag. Auch der Universalkorrektor, mit dem sich synchron alle Kalenderanzeigen, einschließlich des Großdatums, gleichzeitig tageweise weiterschalten lassen, wird im Entwicklungsstadium durch 50.000-faches Betätigen des Korrekturdrückers um mehr als hundert Jahre voraus geschaltet. Nur so lässt sich sicherstellen, dass das ewige Kalendarium in der Praxis auch ewig hält. Das Problem einer solchen Apparatur ist allerdings, dass die Belastung beim Drücken durch einen Finger erheblich größer ist als durch einen Stab, weil ein Finger die Kraft langsam aufbaut, bis er den Widerstand des Drückers überwindet und dann den Knopf mit reichlich Energieüberschuss gegen den Anschlag schiebt. Schlencker simulierte das, indem er die Bolzen auf Federn lagerte und Silikonkappen über die Enden stülpte. Außerdem konstruierte er eine Vorrichtung, die das Uhrwerk während des Tests automatisch aufziehen kann, so dass die Tortur auch am Wochenende fortgesetzt werden kann.
Außerdem besorgte Schlencker eine Klimakammer, die von minus 20 Grad trockener Kälte bis zu 80 Grad feuchter Wärme alle Wetterzonen rund um den Globus nachbilden kann. In ihr wird die Temperaturresistenz des Uhrwerks getestet. Und dann kaufte Schlencker noch ein „Drehmoment-Prüfgerät“, mit dem er messen konnte, wie viel Kraft bei einem Zahnrad ankommt, und wie viel dieses Rad selbst verbraucht. Je weniger Energie dabei verloren geht, desto besser ist es für die Lebensdauer eines Uhrwerks. 93 Prozent Effizienz rechnet man bei einem gut gelagerten Rad. Der Rest ist Reibung und geht in den Verschleiß. Und jeder Prozentpunkt weniger verkürzt die Lebenserwartung erheblich. Besichtigen kann er die Folgen dann mit einer Hochgeschwindigkeitskamera, die in der Lage ist, 10.000 Bilder in der Sekunde zu schießen und schnelle Bewegungsabläufe in allen Details sichtbar zu machen. Mit dem bloßen Auge nicht zu erkennende Fehler, wie das durch die Masseträgheit bedingte „Überschleudern“ von dynamisch beschleunigten und abrupt abgebremsten Teilen – wie dem Großdatum – oder ein mechanischer Konflikt zwischen zwei Teilen, können auf diese Weise aufgedeckt und beseitigt werden. Es ist ein unverzichtbares Diagnosegerät ohne dessen Hilfe auch die Entwicklung des exakt springenden Minutenzählers im DATOGRAPH PERPETUAL nicht möglich gewesen wäre.
Richtig zufrieden war Schlencker trotzdem noch nicht damit. Seine Vision war es, einzelne Baugruppen in einer Uhr überprüfen zu können, noch bevor es überhaupt eine Uhr dazu gab. Denn das Problem im Uhrenbau ist, dass man konstruktionsbedingte Ungenauigkeiten im Gang erst erkennen kann, wenn die ganze Uhr bereits fertig ist. Besonders problematisch ist dabei immer das Zusammenspiel von Spirale und Unruh. Deshalb suchte Schlencker nach einer Methode, mit der sich diese beiden Komponenten exakt aufeinander abstimmen ließen. Ohne den störenden Einfluss des restlichen Räderwerks. Notwendig war dazu ein Gerät, das nicht nur die Anzahl der Schwingungen messen kann, die ein Unruhreif pro Minute macht, sondern auch wie weit der Reif in beide Richtungen schwingt, weil erst die Amplitude Auskunft gibt über die Kraft hinter der Schwingung.
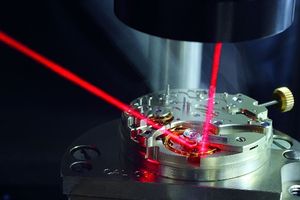
Schlencker brauchte also einen Laserstrahl, der einen schwingenden Reifen permanent abtastet und dabei die Ausschläge zählt und dann noch die Amplitude misst und das am besten in jeder denkbaren Position, um die unterschiedlichen Einflüsse der Schwerkraft zu simulieren. Außerdem brauchte er eine Software, die all diese Daten umrechnet in aussagekräftige Kurven. Drei Jahre dauerte die Entwicklung, dann hatte Lange ein „Schwingungsmessgerät“, wie die Apparatur offiziell heißt. Es war ein echter Meilenstein. Zum Einsatz kam das Gerät auch bei der Entwicklung des DATOGRAPH PERPETUAL. Für diese Uhr entwickelten die Konstrukteure eine genau für diesen Uhrentyp optimierte und im eigenen Hause komplett gefertigte Unruhspirale, die dem Werk optimale Gangstabilität verleihen sollte. Verschiedene Modelle aus dem Prototypenbau wurden mit dem Schwingungsmessgerät getestet und mit der Unruh abgestimmt, bis ein perfektes Ergebnis vorlag. Und diese Messungen wurden dann noch einmal mit der fertigen Uhr wiederholt. Die Mühe hat sich gelohnt. Die mittlere Gangabweichung lag beim DATOGRAPH PERPETUAL zwischen 0,5 und 2 Sekunden pro Tag. Normalerweise gilt schon ein Wert unter sechs Sekunden als außergewöhnlich präzise.
Organisatorisch gehört das Prüflabor zur Produktentwicklung. In ihm arbeiten die besten Uhrmacher im ganzen Land. Menschen, die Probleme lieben, über logische Qualitäten und physikalisches Wissen verfügen und umfassende Kenntnisse haben von allen Uhren der Manufaktur. Und die das ertragen, was jeden leidenschaftlichen Uhrmacher am eigenen Körper schmerzt: einer 100.000-Euro-Uhr mit dem Hammer auf den Kopf zu hauen.
Quelle: Lange Uhren GmbH